Concrete Resurfacing vs. Replacement: Choosing Whether to Repair
11 minutes read
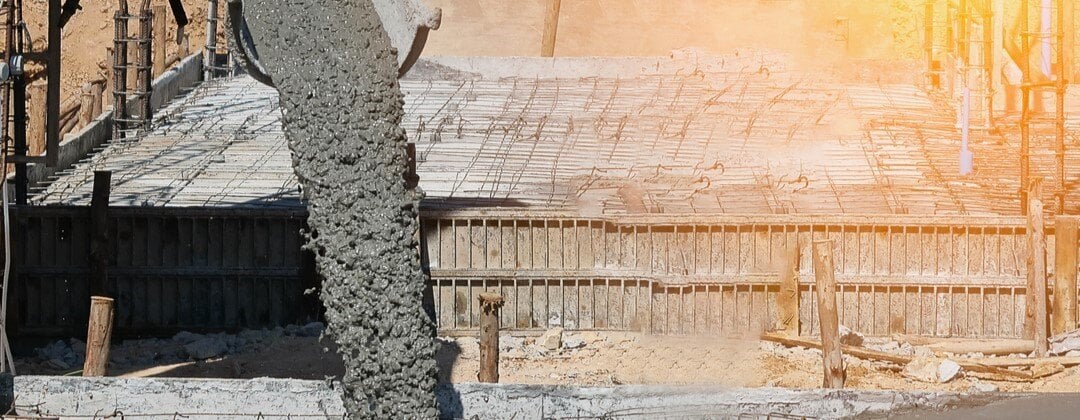
Commercial concrete structures might be built to last for decades … but what if problems show up sooner?
Ideally, solid, well-maintained concrete can last over 50 years. Still, daily wear from heavy traffic and exposure to the elements can take a toll. The NYC parking garage collapse — and the discovery of 4,000 at-risk garages across the five boroughs — highlight why annual structural evaluations are so important.
For contractors, the choice between concrete resurfacing vs. replacement is a constant debate. It’s a fine line to walk, affecting everyone involved, from subcontractors to property owners. Cost, timing, and the overall impact on the structure all come into play. In this article, we’ll explore the pros and cons of each approach and suggest some key questions to guide your choice.
With safety and longevity on the line, it’s worth taking a closer look at the best path forward.
4 Options for Repairing or Replacing Concrete
Once you recognize a slab of concrete has seen better days, the gears in your head should start turning before it turns into a safety issue. Should you renew or extend the life of the floor, deck, or other installation? Or start from scratch?
There are four options; each works best with different issues or degrees of damage:
- Repairing
- Resurfacing & Overlays
- Raising
- Replacing
Repairing
Repairing concrete involves fixing specific issues such as cracks, chips, or small holes without redoing the entire surface. You can limit your work to repairs when the structural integrity of the concrete is largely intact, and the damage is localized. The process typically includes three steps:
- Rebar – Replacing unsalvageable supports; coating or reinforcing partially deteriorated bars
- Patching – Following the manufacturer’s instructions for mixing, getting air pockets out of the mixture, and applying product to the cracks
- Finishing – Smoothing the surface with a trowel, letting the mixture set, and feathering edges or otherwise matching the repaired area to the existing concrete
- Sealing – Uses polyester, epoxy, or another material to prevent leaking from the cracks
Resurfacing & Overlays
Concrete resurfacing involves applying a thin layer of cement on top of the existing surface. This method is chosen when:
- The concrete still has structural integrity
- Fading & imperfections are detracting from the appearance
- Slight damage is present
Concrete resurfacing products rejuvenate the appearance and extend the life of concrete without the cost of full replacement.
Concrete overlay products are thicker and more robust materials. And there’s a whole lot of ‘em, from stamped to self-leveling to polymer-modified overlays.
Use these to:
- Correct more substantial damage
- Improve wear resistance
- Add a decorative touch
Structural concrete overlays use more advanced technology than simple resurfacers, making them viable for protecting heavy-duty floors and other commercial surfaces.
Raising (or Slabjacking)
Raising, aka slabjacking or mudjacking, is a repair method that lifts and levels sunken or uneven concrete slabs. The process involves pumping a grout mixture or a polyurethane foam under the slab to raise it to its original position.
Concrete raising is exclusive to slab-on-grade applications.
If you need a cheaper alternative to replacement for addressing unevenness or subsidence – without disturbing the structure – raising is an option. However, if the surface has sunk 8” or more, replacement will be necessary.
Replacing
Replacement – aka full-depth repair – involves removing the old concrete entirely and pouring anew. This method is necessary when the concrete has extensive damage or structural problems, or when repairs and resurfacing are no longer viable solutions.
Replacement is the most invasive and typically most expensive option, but it might be the only solution for ensuring safety and functionality.
Factors that Influence Repairing Cracks in Concrete
Each concrete repair job is different. Look closely at each factor that might influence the cost, length, and long-term outcome of your work:
- Level of structural damage
- Budget
- Age
- Future use & load requirements
- Regulations & certifications
- Aesthetics
- Schedule
1. Level of Structural Damage
Typically, one of two scenarios leads you to the point of discussing concrete replacement or resurfacing:
- Trigger event: If a user loses money or suffers an inconvenience, you’ll hear about it. An example: the manager of a commercial garage receives a complaint after a falling chunk of concrete damages a user’s car. The manager contacts a contractor, who employs stopgap measures until an evaluation is complete and it’s ready to tackle a full fix.
- Annual evaluation: Regular examination of the structure shows cracks or other signs of structural issues.
Repair works well for small holes, but the presence of large holes or a large number of holes means a short-sighted fix wont’ last long. The rule of thumb is that replacement is necessary if cracks will require more than 2” of material to fix, or if it’s sunk more than 8”.
Below are a few more questions to help with your concrete repair and replacement decisions:
Damage Concern |
If Yes, Then … |
Can you return the concrete to its original integrity? |
Repair it |
Is there spalling? |
Replace it |
Is delamination the main concern? |
Repair it |
Is there a lot of material missing? |
Replace it |
Is the subbase eroded? |
Replace it |
If the subbase is solid, your choice may come down to pricing. If there’s too much material missing, you’ve got a structural issue that probably merits replacement.
Safety for those who are handling the repairs and those who are regular visitors should be the first priority.
2. Budget
From a cost standpoint, repairing concrete is often less expensive than replacing it. However, if the damage is extensive or the area is prone to recurring issues, replacement might be more cost-effective in the long run.
There's a widely accepted threshold in commercial concrete replacement. While not necessarily an official standard, the best practice is that a repair requiring more than two inches of material means the more cost-effective choice is to replace the concrete pad.
Consider the total cost of ownership when deciding between repair and replacement. From an owner's standpoint, it makes more sense to find a way to fully replace it. This typically provides the longest break between investments in repairing cracks in concrete. However, it is not always the most effective choice at the moment.
3. Age of Concrete
Concrete is super tough and lasts a lot longer than most materials, but it doesn't last forever. If you've had a concrete surface for about 20-25 years, it's time to plan for repair or replacement.
Remember, exterior concrete gets hit by weather a lot more than inside materials do. Outdoor concrete almost always has a shorter life span. Make plans for replacement accordingly if the concrete has been exposed to extreme weather conditions for an extended period.
4. Future Use & Load Requirements
Concrete that’s withstood run-of-the-mill traffic for years might be a candidate for repair – provided the issues aren’t extensive. However, if the usage intensity or load requirements are expected to increase, replacement might be more beneficial than repairing the existing structure.
One example of this is a garage floor where previously it only had to support a car or two. However, future plans include the installation of a lift, and manufacturers recommend 4” of 3,000 lb. concrete to support the heavy machinery.
(Pro Tip: Verify the structure will still have enough clearance if you add a layer.)
5. Regulations & Certifications
In some cases, choosing replacement vs. repair might be the only way to meet current building codes and standards. This will be location-specific.
An inspection typically triggers repair work, which isn’t necessarily a bad thing on its own. When you’re having an inspection because something already collapsed or suffered serious damage, that’s a bad thing.
|
6. Aesthetics
For some projects, the appearance of the concrete is as important as its structural integrity. While repairs can often blend with the existing concrete, they might still appear patchy and inconsistent. In the event you have a very ornate design in the concrete, replacement might be the best route.
Visual considerations include:
- Curb appeal’s impact on property’s value
- Historic significance of the “look”
- Whether advances in color matching & texturing can sufficiently limit discrepancies
7. Schedule
Obviously, repairing concrete is typically faster than replacing it, which is crucial when the project schedule is tight. If that’s your case, repairing might be the preferable option – just don’t compromise on structural integrity in the process.
What’s your estimated amount of time the structure would be inaccessible in the case of replacement? What about for simpler repairs? All involved parties should discuss the downtime associated with each choice.
FAQs: Concrete Resurfacing vs. ReplacementYou’re not the only one walking the fine line. Here are some of the most frequently asked questions about concrete resurfacing vs. replacement: Q. How does use case, like pedestrian traffic vs. heavy vehicle use, influence the choice between resurfacing and replacement?A: Usage scenarios are a major factor when deciding between resurfacing and replacement, as each setting places different demands on the concrete surface. For areas with pedestrian or light use, resurfacing or overlays are often suitable since these surfaces don’t endure heavy pressure daily. These options can improve the concrete's appearance and lifespan without requiring the structural overhaul that replacement involves. However, areas exposed to heavy vehicle traffic, such as loading docks, warehouses, or parking garages, undergo much more stress. In these situations, resurfacing may only provide a temporary solution, as the weight and friction from constant heavy use can quickly wear down resurfaced layers. Replacement tends to be more practical and cost-effective in these high-load applications, providing a new foundation that withstands significant pressure. Evaluating both current and anticipated traffic patterns can clarify whether resurfacing will be effective or if replacement is a better investment. Q: How does environmental exposure to freeze-thaw cycles, saltwater, or road salt impact the effectiveness of resurfacing and overlays vs. replacement?A: Environmental factors can significantly impact the durability of resurfaced concrete. Freeze-thaw cycles, common in the Northeast, cause water within the concrete to expand, which can lead to cracking and gradual weakening. Resurfaced layers, though capable of refreshing some damaged surfaces, may not perform well in these conditions if the underlying concrete is already compromised. In these cases, resurfacing may only delay an inevitable – and much larger – issue. Salt exposure also wears down concrete surfaces, especially in areas where deicing salts are a must for slippery roads and sidewalks. Salt can increase deterioration by eroding the surface and corroding reinforcing steel. For concrete regularly exposed to salt, adding a protective coating may provide some resilience, but in most cases, full replacement with salt-resistant materials will be more cost-efficient over time. Considering the specific environmental stressors at play can help you pick a method that suits both the location’s needs and the concrete’s exposure levels. Q: Can preventative maintenance extend the life of concrete surfaces after they’ve been resurfaced, raised, or repaired?A: Yes, several maintenance practices can help extend the life of concrete surfaces following any repair, resurfacing, or raising work. Regularly sealing the concrete is one of the most effective ways to protect it, creating a barrier against moisture, chemicals, and wear. Sealants are particularly useful for outdoor concrete surfaces or high-traffic areas where water or contaminants might seep into cracks and weaken the structure. Routine cleaning also helps, removing dirt, salt, and other corrosive substances that can degrade the surface. Additionally, managing water runoff to avoid pooling or freezing is |
Concrete Replacement vs. Resurfacing: One More Thing to Remember
Repairing vs. replacing concrete involves different levels of effort, cost, and downtime. Only you and the property owner know how much you can stomach.
Repairing and resurfacing are less invasive methods that take aim at minor to moderate issues. Raising is specialized work that addresses settlement or unevenness. Replacing concrete is the last (yet common) resort when other methods can’t restore the concrete's structural condition or when aesthetics are key.
Each method has its place in maintaining and extending the life of concrete structures. Don’t make a hasty decision – plan a thorough assessment of the concrete's condition and the project's goals.
Looking for more information on extending the life of your concrete installation? Engaging with structural engineers or concrete product specialists can provide valuable insights on safety and cost. Or, keep learning on your own at our growing blog library: